Idea Bulletin
Programmable, Adjustable, Opposing Milling Modules Upstream design and continuous operation save setup time
Application
A processor of coiled metal wanted to reduce handling time and automate machining operations. The problem was that several different widths and thicknesses of material and hundreds of different milling patterns were combined to produce the company’s thousands of products.
Challenge
Originally the milling operations were done after the material was cut to length. The machine envisioned would position a length of material while still connected to the coil and mill a specific pattern. The company wanted to eliminate the handling and fixturing required for machining after cutting to length.
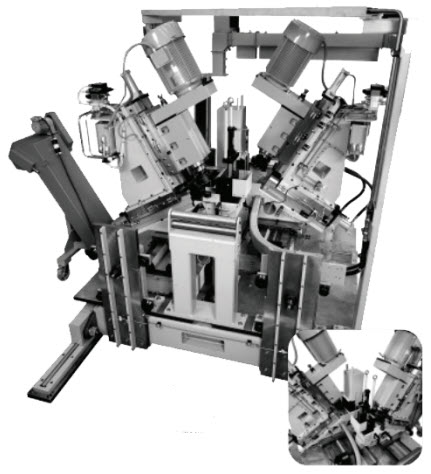
Solution
After intensive analysis of the multiple operations required downstream of the cuttingto-length operations, it was determined that the milling operation would be better performed before the material was cut off from the coil. To
meet all requirements, this custom machine tool was designed to be adjustable in five axes. The material strip is processed continuously as it moves through the machine.
The multi-tooth milling head is first fed into the material in two axes. Second, the material is fed through the machine and into the milling head for the required distance. Belt driven spindles are used for the milling operation. The “Y” and “Z” axes hardened way slides feeding the spindle are controlled by hydraulic cylinders. The “X” axis is a dovetail slide used for manual adjustments of the two spindles relative to each other. The fourth and fifth axes are for adjusting milling angles and material widths. The machine has been a tremendous success. Hundreds of complicated and error prone operations have been eliminated. Productivity has increased, and the company has been able to expand its product offering with no additional machinery or
personnel required.
Cost Savings
Not only is the design and operation of the machine successful, but the Gilman USA components that made it possible are all stock or standard products. This use of existing designs kept the project cost low.
Sales Point
By using stock and started components to achieve the customer’s design goals, cost and delivery time were both minimized.
Technical Specifications
- 2 each HWS12-12-21-H2-3 slide assembly with hydraulic cylinder drive
- 2 each HWL12-22-30-H3-5 slide assembly with hydraulic cylinder drive
- 2 each DC16-19-36-M-E1-15 slide assembly with Acme screw with right angle hand wheel
- 2 each 6500C-X2M-50-SB3 belt-driven, motorized spindle
- The customer provided the angle brackets and assembled the machine on their shop floor
Every care has been taken to ensure the accuracy of the information contained in this publication but no liability can be accepted for any loss or damage whether direct, indirect, or consequential arising out of use of the information contained herein.
Request A Quote
To request a quote, please contact us using the contact form.
Use our product configurator to download a drawing to use in your design.
If you you would like to reach us directly, give us a call at 262-377-2434.