Idea Bulletin
High Speed Dual Spindle Multi-Axis Boring Machine Rigidity of vertical travel improved for faster feed rates
Application
An American motorcycle manufacturer was gearing up for increased production of their large touring motorcycles. Operations required on this dual spindle multi-axis boring machine were center drill and spot face for the first spindle and 1-1/2” boring operations for the second spindle. The material being worked was Timken cast iron.
Challenge
Because the existing 10-year old dual spindle drilling and boring machine could not keep up with the required production rates, the manufacturer decided to replace it. Among the highest priorities for the replacement machine was a design with more vertical rigidity to allow for faster feed rates and thus shorter cycle times.
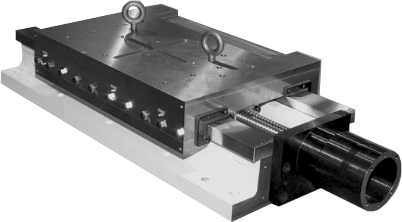
Solution
Through a joint development process including the manufacturer, the machine tool builder and Gilman, a unit was designed that met all of the end-user requirements. The base chosen was a hardened steel way slide with preloaded ground ball screw driven by a single phase motor. A vertical angle bracket supports another hardened steel way slide with preloaded ground ball screw driven by a single-phase motor. Spindles chosen were Gilman model 6500B with a block housing and triplex ball nose bearing arrangement and labyrinth seal. The shaft nose was 50 NMTB taper. The design retained the single motor drive. The customer supplied reduction unit turns the first spindle at 2,900 RPM and the second spindle at 1,950 RPM.
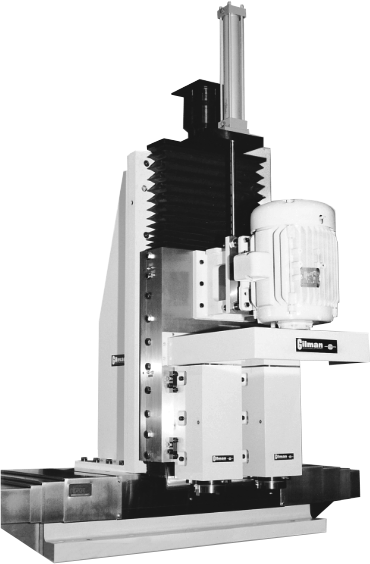
Cost Savings
Factoring in increased production, the machine investment is predicted to begin returning dividends in 18 months. The robust design has a safety factor of 1.5 of current capacity and allows for future improvements in tooling and new materials.
Time Line
Total time from initial concepts to cutting was 14 weeks.
Technical Specifications
6500B Spindle:
• Preloaded Triplex set, contact ball bearings, medium preload 85mm I.D., nose end. Preloaded pair, ABEC 7, 15° angular contact ball bearings, medium preload 70mm I.D., drive end
• Synthetic grease lubrication
• Labyrinth seal each end
• Maximum thrust into spindle 1,695 LBS.
• Shaft supplied with coolant union pilot and threads
• Air purge fitting
HWS24-34-54-SPM2-18 Slide:
• L.H. GIB
• Telescoping steel way covers both ends
• 2.500-.500 R.H. thread
• Ground ball screw - preloaded nut, 1,420 in. LBS. maximum traverse rate
• Saddle width 24”
• Saddle length 34”
• Base length 54”
• Travel 18”
HWL24-34-54-SPM2-16 Slide:
• Accordion way covers drive end
• Steel plated accordion way covers opposite drive end
• 2.000-.500 R.H. thread ground ball screw - preloaded nut, 770
in. LBS. maximum input torque, 350 IPM maximum traverse rate
• Saddle width 24”
• Saddle length 34”
• Base length 54”
• Travel 16”
Every care has been taken to ensure the accuracy of the information contained in this publication but no liability can be accepted for any loss or damage whether direct, indirect, or consequential arising out of use of the information contained herein.
Request A Quote
To request a quote, please contact us using the contact form.
Use our product configurator to download a drawing to use in your design.
If you you would like to reach us directly, give us a call at 262-377-2434.