Idea Bulletin
Filament Winding Spindle Modification Filament Winding Spindle Repair - Air purge spindle modifications cut downtime by 800%
Application
30,000 RPM spindle for spool winding of filament material.
Challenge
Gilman Precision was contacted by a high volume, U.S.-based manufacturer experiencing a critical, premature, bearing-failure complication with their European-manufactured spindles. While their original design had called for 24-month spindle life, actual spindle life was averaging a costly and unacceptable three months.
Gilman engineers were asked to remedy the problem.
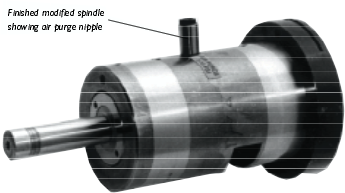
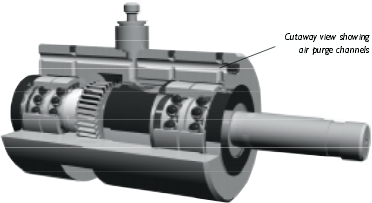
Solution
To determine the cause of shortened spindle life, a team of Gilman engineers interviewed the manufacturer and conducted an exhaustive investigation of parts, processes and environmental conditions. The “customer- manufacturer” investigation team concluded the following: during the 30,000 RPM filament winding operation, fine dust-like particles of filament material were becoming airborne. Upon entering and contaminating the bearing chamber, these particles were creating friction and destroying the bearings. After isolating the cause, Gilman engineers offered a creative solution to increase spindle life: they modified the housing by drilling passageways to allow for low-pressure, clean, dry air to be pumped into the bearing case, pressurizing the area. The pressurized airflow forced the contaminants out of the bearing case, achieving a substantial increase in spindle life consistent with the customer’s original 24-month specification. With the contamination problem solved, the spindle was repaired. Finally, Gilman Spindle Service proposed a phased replacement program to ensure that the hundreds of spindles involvedin the filament winding process were modified on a systematic basis, sparing the costly inconvenience of shutting down production.
Spindle Modification Process
• Disassembly and inspection of spindles
• Inspect shaft-bearing journal diameters - Front- bearing journal diameter .6693 ± .0001; Rear-bearing journal diameter .5906 ± .0001 Rear journal concentric to front journal within .0001 TIR
• Inspect housing-bearing bores - Front- bearing bore diameter 1.3779 ± .0002; Rear- bearing bore diameter 1.2599 ± .0001; Front bore concentric to rear bore within .0001 TIR
• Re-manufacturing spindle parts as necessary and in-line tolerances brought back into specifications for Class 7/9 bearings
• Air-holes drilled in the spindle casing for pressurization
• Make spacer, replace laminar ring seals, make front- bearing nut and replace bearings
• Each spindle receives a run-off test and carries a new spindle warranty upon leaving the Gilman Service Center
Every care has been taken to ensure the accuracy of the information contained in this publication but no liability can be accepted for any loss or damage whether direct, indirect, or consequential arising out of use of the information contained herein.
Request A Quote
To request a quote, please contact us using the contact form.
Use our product configurator to download a drawing to use in your design.
If you you would like to reach us directly, give us a call at 262-377-2434
.