Case Study: Gilman Optimizes F35 Strike Fighter Aircraft Landing Gear with Specialized Five-Axis Machine Module
Manufacturers developing equipment and parts for the US Military are subject to some of the industry’s most demanding engineering specifications and regulations.
Knowing these demanding specifications, a US Military Contractor reached out to Gilman’s engineers to create a machine to manufacture components for F35 strike fighter landing gear, which had numerous unique challenges, including the not-so-easy task of boring a titanium block.
US Military-Approved Precision
The Military Contractor worked with Gilman Precision to create a unique compound assembly that could manufacture components to meet the specifications of F35 strike fighter landing gear. This project was particularly demanding for several reasons:
- The machining target is not defined by x, y, or z coordinates. Instead, it is spatial.
- Gilman engineers had to bore a titanium block to locate the landing gear.
- Ultra-precision, smooth motion, a vibration-free spindle, and a multi-axis positioning system were required.
Gilman Precision supplied a five-axis linear guide assembly with a belt-driven spindle to perform this difficult operation. There are two axes of rotary motion and three axes of linear motion. The slide units are driven with ball screws and fitted with way covers to keep the ball screw and linear guides clean.
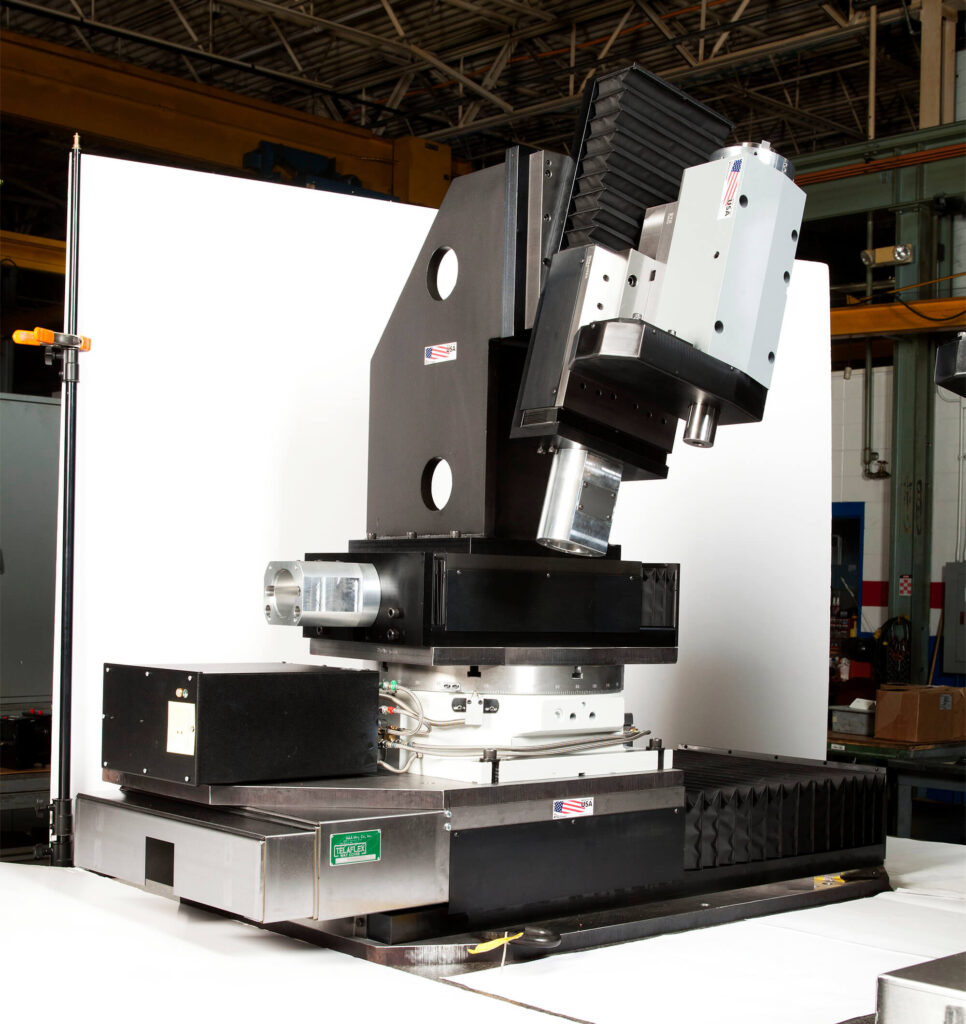
Custom Spindle Designs: Collaborating with the Gilman Engineers
Close collaboration is vital to a successful compound assembly project. Gilman worked closely with the wing frame engineers to define the axis accuracy requirements and ensure the design physically fit their needs.
Gilman is dedicated to their clients and goes the extra mile to develop and deliver on the provided specifications. No project is too complex for their team of engineers, who are happy to assist, from concepts to detailed designs.